Overview:
- New multi-building retirement community on 108-acre site
- There are 3 separate “Neighborhoods” on the site; with each Neighborhood consisting of a Community Building
- Each community building are four to five (6-7) story residential buildings, miscellaneous parking structures and other support functions
- Construction cost of $250 million
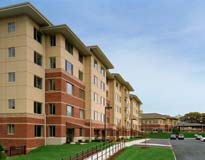
The project involved the construction of a new multi-building retirement community on a 108-acre site located in Hingham, MA. There are 3 separate “Neighborhoods” on the site; with each Neighborhood consisting of a Community Building providing power, emergency power, communications, cctv, cable tv and building heating/cooling for its respective neighborhood. Surrounding each community building are four to five 6-7 story residential buildings, miscellaneous parking structures and other support functions. Neighborhood 1 was occupied in 2006. Neighborhood 2 has been 80% occupied since 2008. Neighborhood 3 is currently at the Schematic Design level and awaits development at a later date.
This project included the design of a complete infrastructure to support these buildings, including power, data, communications, water, sewer (including an on-site wastewater treatment plant), natural gas and storm drainage.
The HVAC design for each neighborhood consists of a centralized water source heat pump system. The system consists of (2) 2000 gpm, fan-less, ejector type cooling towers, and (12) high efficiency modular boilers, totaling 12,000,000 btuhs. The boilers are also used to generate domestic hot water. Condenser water is circulated throughout the neighborhood buildings with a combination of (3) 100 horsepower, horizontal split case pumps. The Community Building HVAC is accomplished with commercial grade, vertical water source heat pumps located within individual mechanical rooms.
The Plumbing design for each neighborhood includes domestic water, sanitary waste and natural gas. Community Building hot water needs are met by storage tank heaters with integral shell and tube coils for using boiler hot water to generate domestic hot water. The Residential Buildings generate hot water by means of indirect fired gas water heaters and multiple storage tanks with complete recirculation to maintain temperatures. Building wide recirculation systems are provided for the Residential Buildings. Depending upon the number of units in a Residential Building, domestic hot water may be generated in an adjacent, connected Residential Building. Residential Building Living Unit bathrooms can be converted from tubs to showers. Piping is provided in the walls to facilitate this conversion. All sanitary waste flows by gravity to the site sanitary sewer system. At the Community Buildings, point-of-use interior grease traps, as well as a “house” grease trap on a dedicated sewer, are provided for the Kitchen grease lines. Due to the on-site wastewater treatment plant, a special “holding tank” is provided on a dedicated line outside the building, to collect waste from the hair salon’s wash sinks. City water pressure serves most building without use of booster pumps. Parking structure design included drainage, with lower levels connected to the sanitary sewer system through MWRA gas/sand/oil interceptors. The upper level, at grade, drainage connects to the on-site storm system through engineered separators. The projected overall construction costs are $250 million.